Las aleaciones de Aluminio- Litio
No es nueva; pero sin embargo ha sido recuperada –entre otras- por la industria aeronáutica por sus especiales características
Las aleaciones de Aluminio-Litio fueron desarrolladas por los productores de aluminio (a partir del año 1910), con el objetivo de conseguir para el sector aeronáutico una línea de productos que permitieran, principalmente, reducir el peso (menor densidad) en elementos estructurales de aviones; a la que posteriormente se unió la industria aeroespacial (por ejemplo en aplicaciones criogénicas como los tanques de oxígeno e hidrógeno líquido, para impulsores).
También se perseguía obtenerlo a partir de los equipos ya disponibles con el objetivo de conseguir un coste competitivo para que los fabricantes pudieran sustituir directamente las aleaciones de aluminio convencionales utilizadas (que generalmente constituye entre el 70 - 80% del peso de los aviones).
Fruto de todo ello fue el desarrollo (e introducción) de las aleaciones 8090, 2090 y, 2091 a la que se unió a mediados de 1980 la Weldalite 049 y posteriormente la CP 276. Son aleaciones comercialmente disponibles actualmente aunque están siendo progresivamente sustituidas por la nueva generación de aleaciones Al-Li
Las nuevas aleaciones presentan contenidos inferiores en litio que a pesar de no aprovechar tanto la ventaja de la ligereza ofrecen una microestructura y propiedades más adecuadas para aplicaciones en la industria aeronáutica. Las nuevas aleaciones como el AA2094, AA2096, AA2199, AA2196 y AA2050 están basadas en la combinación de los elementos Cu-Li-Mg-Ag-Zr y presentan características de una gran conformabilidad y mejora en la tenacidad y ductilidad. El porcentaje de otros metales presentes en las aleaciones aluminio-litio es:
Weldalite 049 5.4 Cu, 1.3 Li, 0,4 Ag, 0,4 Mg, 0,14 Zr
Aleación 2090 2.7 Cu, 2.2 Li, 0,12 Zr
Aleación 2091 2.1 Cu, 2 .0 Li, 0,10 Zr
Aleación 8090 1.3 Cu, 2,45 Li, 0,12 Zr, 0,95 Mg
Aleación CP276 2.7 Cu, 2.2 Li, 0,5 Mg, 0,12 Zr
Aleación 2050 3,5 Cu, 1 Li, 0,10 Zr, 0,40 Mg, 0,35 Mn
Aleación 2099 2,7 Cu, 1,8 Li, 1, 0,08 Zr, 0,6 Zn, 0,3 Mg, 0,3 Mn
Cada aleación se presenta, asimismo, en diferentes estados de suministro y tratamiento térmico. Planchas y perfiles en diversas dimensiones (y espesores) y tratamientos térmicos diferentes (T3E27, TE328, T41..).
aspectos que hacen ser comerciales las aleaciones Aluminio – Litio
Concebidas como materiales avanzados además de su baja densidad y sus aplicaciones criogénicas se caracterizan por una alta rigidez, tenacidad y resistencia a fatiga . La resistencia a la propagación de grietas de fatiga es superior en comparación con las tradicionales aleaciones 2xxx y 7xxx debido principalmente a la tenacidad manifestada en la punta de la grieta; aunque esta ventaja se reducen en el caso de esfuerzos de compresión donde se producen fatigas de amplitud variable que afectan los valores de ductilidad y tenacidad de fractura en el corte transversal de la anisotropía en plano horizontal. Esta mecánica, fue la que impidió, inicialmente, la sustitución directa de las aleaciones utilizadas en los fuselajes, por aleaciones de aluminio-litio; aunque esta tendencia se está solucionando con el nuevo grupo de aleaciones de aluminio-litio.
física metalúrgia
En el desarrollo de aleaciones de baja densidad, la solución más simple para reducir el peso, es añadir elementos de bajos pesos atómicos como elementos agregados. En el caso de aleaciones de aluminio utilizar litio y berilio resultan ser los más eficaces.
El litio es el elemento metálico más ligero; cada 1% de litio (hasta el 4,2% Li -límite de solubilidad-) reduce la densidad de la aleación en un 3% y aumenta el módulo de alrededor de un 5% . Además, durante el tratamiento térmico el litio llega a formar un precipitado esférico Al 3 Li responsable del incremento de la resistencia mecánica de la aleación por medio del mecanismo de precipitación .
Aleaciones AI-Li-X. Se han realizado diversas modificaciones en la composición química y la fabricación para mejorar ductilidad y dureza, manteniendo al mismo tiempo una elevada tenacidad. Los resultados de los ensayos señalan que cobre, magnesio, circonio han demostrado tener efectos beneficiosos. Magnesio y Cobre mejoran la tenacidad; el Circonio (que constituye la AlZr ) estabiliza la estructura de grano y suprime la recristalización.
Comparando con formulaciones tradicionales, las aleaciones de aluminio (AI-Li-X) muestran una tenacidad mayor (del orden 7 al 12%); que equivale a decir mayor resistencia a la propagación de grietas de fatiga y mejor dureza a temperaturas criogénicas.
También los ensayos muestran que la fatiga puede sufrir una aceleración y por extensión de las grietas (cuando son estructuralmente micro pequeñas), la fluencia -en las grietas- tener unas tasas de crecimiento en las aleaciones Al-Li-X (que pueden ser más lenta o superiores a los aluminios convencionales), en función de su orientación cristalográfica.
Así el crecimiento de las grieta del AI-Li 8090 en el sentido transversal longitudinal a la orientación (en el plano de la grieta su crecimiento va en dirección paralela a la extrusión) son más elevadas que en las aleaciones de aluminio 2219 y 2124. Por el contrario en sentido longitudinal transversal a la orientación (plano de grieta y su crecimiento en dirección perpendicular al sentido de la extrusión) son muy inferiores.
O dicho en términos de su precipitación parece ser que el único efecto de magnesio es una reducción de la solubilidad del litio que afecta a este comportamiento. La microestructura de una aleación de aluminio-litio -magnesio en las primeras etapas de envejecimiento es similar a la del aluminio-litio.
aplicaciones de las actuales aleaciones AI-Li-X
Durante 1980, los fabricantes de aluminio, trabajaron en aluminio-litio como sustitutos de los tradicionales aluminios; dando lugar a la aparición de las aleaciones comerciales 8090,2090 y 2091 y la introducción posterior de Weldalite 049 y CP276.
Los fabricantes producen sus aleaciones pero no están –globalmente- suficientemente bien definidas en cuanto a características y composición. Por ello es adecuado contactar con la Asociación del Aluminio y en materia aeroespacial consultar las normativas publicadas por SAE Internacional para obtener información sobre el registro actual de aleación de especificación y sus propiedades.
-Aplicaciones comerciales en primer lugar la aeronáutica donde se encuentran grandes componentes como en las alas (bordes, estructura y recubrimiento); fuselaje (armazón y cubiertas); pistas de asiento así como gran número de componentes de diversos tamaños que forman parte del avión.
El grafico proporciona algunas indicaciones de los literalmente cientos de kilos de piezas de aluminio-litio que pueden ser/están diseñados en una aeronave nueva o ya existente. Además de los usos comerciales conocidos - no hay que olvidar que existen otras muchas para helicópteros, transporte, etc. -que están en producción y estudio, existe un importante capítulo de elementos que se encuentran bajo el régimen de la confidencialidad lo cual limita el conocimiento su volumen.
En estos ejemplos de aplicación juegan un importante papel requisitos tales como resistencia, rigidez, peso mínimo, comportamiento ante la corrosión.
tecnología espacial. De todos los beneficios, el ahorro de peso es la más destacada en las aplicaciones espaciales. También se integran en estructuras rígidas básicas, depósitos y como forma metalúrgica (a partir de planchas) entre otras, la construcción de pantallas térmicas (2090-T81) por su comportamiento criogénico.
Las propiedades criogénicas del 2090-T81 se han estudiado ampliamente. Aunque los primeros datos de las pruebas revelaron que podría haber incompatibilidad con oxígeno líquido; posteriores ensayos realizados por el Instituto Nacional de Ciencia y Tecnología ha puesto de manifiesto que las aleaciones de aluminio-litio –como el 2219- eran compatibles con entornos de oxígeno líquido.
fabricación de productos de aluminio-litio
Aunque básicamente los procesos como laminación, extrusión, forja son comparables a las que se realizan en las aleaciones de aluminio convencionales, existen algunas diferencias especialmente en la producción de lingote y el reciclaje. Existen otros efectos como:
- Inestabilidad al agua. La potencial explosión de una fundición en contacto con el agua es mucho mayor que en las aleaciones de aluminio fundido convencional.
Están relacionadas por una serie de variables entre ellas contenido de litio de la aleación, temperatura del metal,.. Cualquier operación con aluminio fundido (es decir de 500- 600ºC ) plantea un riesgo de explosión en presencia de agua.
- Potencial de explosión (incendios). Al igual que el polvo de cualquier aleación de aluminio-litio en concentración suficiente es explosivo en presencia de una fuente de ignición. Además, las aleaciones de aluminio puede generar hidrógeno en presencia de agua y que también puede ser explosivo en presencia de una fuente de ignición. El hidrógeno en espacios cerrados, es particularmente peligroso.
- Efectos del calor en superficie. Durante el calentamiento de las aleaciones aluminio-litio a temperaturas elevadas (> 260 ºC), se produce una oxidación superficial generándose óxido e hidróxido de litio. La formación de estos compuestos es motivo de especial preocupación ya que, a efectos prácticos, afectan la soldadura y la mecanización posterior.
denominaciones de las aleaciones aluminio litio
El desarrollo de aleaciones con aplicaciones comerciales de aluminio-litio (como ya se ha indicado) se inició con la adición, además, de cobre y magnesio. Esta han sido elegidas para superponer a la precipitación el endurecimiento como característica. De esta manera surgieron las aleaciones de 2020 (AI-Li-Cu-Cd), 01429 (Al-Mg-Li), 2090 (AI-Cu-Li), 2091 y 8090 (Al-Li-Mg-Cu) última evolución. Asimismo, comercialmente se incorporaron Weldalite 049 y CP276.
A continuación se especifican algunas características de estas las aleaciones.
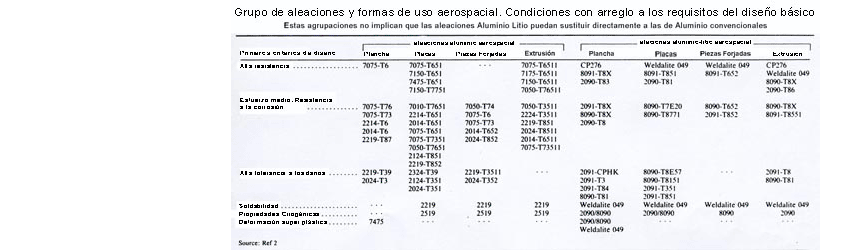
Weldalite 049
Desarrollada por los laboratorios Martin Marietta para aplicaciones aeroespaciales soldadas y con el objetivo de sustituir a las aleaciones base 2219 y 2014.
Se emplea para la construcción de los tanques de combustible de los propulsores y que constituyen la mayor parte del peso seco de los sistemas de lanzamiento espacial. Estos tanques –de combustible y oxidante- trabajan bajo presión conteniendo hidrógeno y oxígeno que al estar en estado liquido requieren que las propiedades criogénicas del material sean un factor casi definitivo para su aplicación en los sistemas de lanzamiento. Además, destacan:
- Resistencia mecánica y tenacidad. Su comportamiento a las temperaturas criogénicas es un aspecto muy importante en comparación con el convencional 2219 ya que la resistencia del Weldalite 049 se mantiene relativamente constante a esas temperaturas. Esta aleación tiene una densidad de 2,7 g/cm 3 .
Aplicaciones. La fabricación de un prototipo –a escala –de un tanque criogénico fue un gran éxito al que contribuyeron propiedades tales como resistencia tanto a temperatura ambiente como criogénicas y buena soldabilidad. Se utilizó, inicialmente, como un material estructural base para sistema de lanzamiento avanzados como el Plan Nacional Aerospacial Titán (y sucesivos desarrollos de esa serie)
Aleación 2090
Desarrollado para ser una aleación de alta resistencia. Ofrece un 8% menor densidad y módulo de elasticidad 10% superior a 7075-T6, una de las principales aleaciones de alta resistencia utilizadas en las estructuras de aeronaves. La aleación 2090 – suministrada en forma de chapa y perfil extrusionado - se utiliza en aplicaciones en las que se solicitan alta resistencia. Además cuenta con excelente soldabilidad y propiedades criogénicas la hacen adecuadas en estructuras que precisen de esas propiedades. También se adecua a aplicaciones que requieran elasticidad; como recubrimientos de alas.
- Resistencia y tenacidad. Su comportamiento es similar a la de otras aleaciones 2xxx y 7xxx; aunque algunas de las formas en que se suministra el 2090 muestran una mayor resistencia a las altas temperaturas con relación a las aleaciones convencionales. Los cambios en la dureza y la gran resistencia a temperaturas criogénicas son más acentuadas en 2090 que en las aleaciones de aluminio convencionales.
Consideraciones de diseño. En general, sus características para ingeniería son similares a las actuales 2xxx y 7xxx. Sin embargo, algunas características de los productos de la 2090 varían y deben tenerse en cuenta durante el diseño y el proceso de selección de materiales:
- el plano de anisotropía que influyen en las propiedades de resistencia a la tracción es mayor que en las aleaciones convencionales. En 2090, las de más importancia se corresponden a los 45 ° que mejoran las propiedades de cizalla.
- Excelente comportamiento de la fatiga (crecimiento de las grietas). Sin embargo, la gran ventaja de 2090 en comparación con las aleaciones convencionales se reduce en el caso de alta sobrecargas o ciclos que predomina la compresión.
- Con el trabajo en frío se obtiene los máximos rendimientos (óptima aplicación propiedades). Esta característica de la 2090 es similar a 2219 y 2024. Fatiga. El rendimiento de 2090 es comparable al de 7075-T6 hasta 105. Mecanizado. Los resultados de las pruebas de maquinabilidad realizadas en una placa de 2090 son comparables a los obtenidos con en las aleaciones 2024 y 7075-T351-T651.
La maquinabilidad se caracteriza por rizado y/o rotura fácil de la viruta y buen/excelente acabado. No obstante, en los ensayos realizados en mecanizado han demostrado que hay que tener ciertas precauciones en el 2090: - La parte debe estar bien apoyada y fijada con un adecuado sistema de amarre. La pieza debe apoyarse perfectamente durante el mecanizado.
- Corte con ángulo positivo; propio de las herramientas específicamente diseñadas para el mecanizado de aluminio que son las utilizadas.
- La refrigeración debe ser continua a la zona de corte.
aleaciones 2091
Se desarrolló para tener resistencia al desgaste, con una densidad un 8% menor y 7% más de módulo que el 2024-T3; una de las que cuentan con mayor resistencia y que puede tolerar mayores esfuerzos por lo que se utiliza en la mayoría de estructuras de aviones.
Se emplea de estructuras secundarias en el que la condición de alta resistencia no sea crítica. La composición química de la aleación 2091 está registrada en la Asociación de aluminio; con una variedad de estados para ofrecer combinaciones útiles de fuerza, resistencia a la corrosión, resistencia al desgaste, ... La microestructura de 2091 varía de acuerdo al espesor del producto y aplicación; en general, los espesores de más de 3,5 mm tiene microestructura recristalizada y los gruesos inferiores con estructura de grano recristalizado alargado.
Las propiedades de 2091 tras elevadas temperaturas de exposición (~ 125 ° C) son relativamente estable. Los cambios de propiedades durante la vida útil de un componente son aceptables para la mayoría de aplicaciones comerciales.
Fatiga. Aunque los ensayos de fatiga en el 2091 se han hecho por diversos laboratorios, productores y usuarios, los resultados han sido difíciles de unificar; pero, en general, el consenso es que, en circunstancias similares, las propiedades de fatiga de 2091-T84 son adecuadas para que pueda ser utilizado como un sustituto de 2024.
aleación 8090
Aleación 8090 fue desarrollada para tener resistencia al desgaste, tenacidad media y una densidad inferior (10%) y un módulo mayor (11%) a los de las 2024 y 2014, de uso común y para aplicaciones donde estas características son fundamentales.
La aleación se suministra en forma de láminas, chapas, extrusiones y piezas forjadas; además para aplicaciones de soldadura. Su composición química está registrada por la Asociación de Aluminio.
Se han desarrollado una variedad de estados que ofrecen diversas combinaciones de fuerza, resistencia a la corrosión, desgaste-resistencia y capacidad de fabricación. En sus propiedades físicas típicas, las placas extrusiones, forjados tienen un microestructura recristalizada que influye en el desgaste-resistencia y una mayor tenacidad.
Consideraciones de diseño. En general, la aplicación del aluminio-litio son similares a las del aluminio 2xxx y 7xxx utilizadas por la industria aeroespacial. Sin embargo, como el 2090, deben ser tenidos en cuenta algunos factores cuando se utiliza 8090:
- El plano en la anisotropía de las propiedades de resistencia a la tracción de algunos productos (placas, extrusiones, las piezas forjadas) es mayor en 8090 que en aleaciones convencionales.
- En trabajo en frío se obtienen buenos resultados (en menor medida que con el 2090).
Fatiga. El comportamiento del crecimiento de la grieta es mejor; aunque en el diseño se ha de tener en cuenta el impacto del estrés y las sobrecargas.
En planchas, la tasa de crecimiento de las grietas de fatiga 8090-T81 es más lento que en el de 2024-T3. Parece ser que su microestructura tiene algún efecto sobre la fatiga; una estructura alargada recristalizada ofrece los mejores resultados; proporciona la mejor combinación de resistencia y tolerancia daños.
Aleación 2050
La aleación Al-Cu -Li-Mg 2050 ha sido desarrollada como alternativa a placas de espesor medio de aleaciones como el 7075-T7451 o placas más delgadas de la aleación 2024 presentando una de menor densidad y mayor resistencia a la corrosión. Presenta un contenido máximo en litio del 1,3% con el fin de evitar la formación de la fase Al 3 Li considerada perjudicial para la estabilidad térmica. La densidad de la aleación es 2,70 g/cc y además de Cu como elemento que proporciona endurecimiento por precipitación de Al 2 Cu y fases Al-Cu-Li durante el tratamiento térmico contiene Mn y Zr para promover la precipitación de fases que favorezcan una estructura no recristalizada. Por su parte la plata es añadida para promover la nucleación de la fase Al 2 CuLi. La aleación 2050-T84 ha sido aprobada por Airbus para sus modelos A380-800 y A380- 800F para las estructuras inferiores de componentes de sus alas.
R. Broqueta
VACUTREM S.A.
Tel. 93 206 11 02
Fax. 93 570 50 34
www.vacutrem.com
Pedro Egizabal
TECNALIA-Div. Industria y Transporte
Foundry Unit (Unidad de Fundición y Siderurgia)
Tel. 902 760 002
From abroad:+34 943 105 115
Fax: +34 943 003800
e-mail: Pedro.Egizabal@tecnalia.com
www.tecnalia.es
Fuente: ASM |
|
|