|
|
|
|
|
|
home |
S.A. Metalográfica: Fco. Borrego, Simón Barcelona, Désirée Viladot
Universidad de Barcelona: Dra. Núria Llorca |
|
tabla de durezas |
|
|
Tratamiento térmico de moldes para fundición inyectada en hornos de vacío
Estudio microestructural y de características mecánicas
En el tratamiento térmico de herramientas, moldes y matrices, el temple a alta presión con parada isotérmica es la solución más eficaz, al obtener una elevada transformación y una baja distorsión.
La última generación de hornos de vacío, permite la utilización de este sistema que hasta ahora sólo era posible en los sistemas de sales o similares, añadiendo a las ventajas ya conocidas del tratamiento al vacío (ausencia de cambio químico superficial, control de procesos de calentamiento, automatización sencilla del proceso), el modo de enfriamiento martempering en condiciones como mínimo iguales a las de los sistemas de sales. Vamos a comparar los resultados de distintos tipos de tratamiento, contrastando los aspectos críticos microestructurales (precipitación de carburos y concentración de bainitas en el borde de grano), mediante técnicas de microscopía óptica y electrónica, con el control de resilencia, velocidad de propagación de grietas (KIC). Este trabajo sirve como base para el desarrollo de un sistema que permita la obtención de orientación en la duración de la herramienta nalizada (confirmando la bondad de los procesos modernos de tratamiento térmico) y se enmarca en un proyecto europeo CRAFT “TOOLSLIFE” Nº G6ST-CT-2000-50047 (Nueva Metodología de Control Metalúrgico de Herramientas, Elementos y Equipos de Altas solicitaciones en Servicio, en orden a garantizar su tiempo de Servicio), del cual S.A. METALOGRAFICA ha sido la empresa impulsora de este proyecto de I+D+i.
Grietas por fatiga térmica: causas de fallo en herramientas de trabajo en caliente
Es bien conocido que la vida útil de una herramienta de trabajo en caliente, como por ejemplo los moldes de fundición inyectada, está limitada por la formación de grietas de fatiga térmica y termo-mecánica que se forman en la superficie de trabajo de la herramienta y progresan con mayor o menor rapidez llegando a provocar en algunos casos fallos catastróficos de la herramienta con rotura prematura de la misma.
En cualquiera de los casos, la mayor solicitación tanto térmica como mecánica de la herramienta, se produce en la superficie de trabajo de la misma, en primer lugar debido a las condiciones cíclicas de compresión y relajación producidas por el tipo de trabajo realizado y en segundo lugar debido al sistema de enfriamiento tanto interno como superficial de la herramienta, después de cada inyección u operación de estampación. Baste como recordatorio de la violencia de trabajo realizado, los valores de incremento de la presión que se producen en un ciclo típico de inyección de aluminio a doble pistón
Tal como se aprecia la fase de llenado del molde se produce en 0,1 segundos, a una presión de 55 bar, llegando hasta 70 bar de almacenamiento cuando no actúa el multiplicador, o hasta 210 bar cuando actúa el multiplicador. El tiempo total hasta la descarga oscila entre 1 y 2 segundos.
Teniendo en cuenta que la temperatura de inyección del aluminio en el momento de entrar en el molde oscila alrededor de los 600ºC y que el desmoldeo se produce a temperaturas inferiores a 300ºC, es fácil imaginar el choque térmico, repetitivo cada pocos segundos, a que está sometida la piel del molde de inyección lo cual comporta a su vez un choque mecánico producido por el efecto de dilatación y contracción del resto del molde e incrementado por los esfuerzos de presión y descompresión hidráulica producidos al efectuar la inyección del material. Todo ello comporta que el material con el que está fabricado el molde deba responder a las y solicitaciones siguientes:
· Térmicas. Debe resistir las temperaturas de inyección sin sufrir merma importante en sus características dimensionales y mecánicas.
· Mecánicas. Debe soportar esfuerzos de presión de inyección sin que estos sobrepasen el límite elástico y sin presentar fenómeno de fluencia o “creep” excesivo.
· A la fatiga. Dada la frecuencia a que se produce la inyección, los esfuerzos son cíclicos y puntuales, combinados además con cambio rápido de temperatura, por lo que el material del molde está sometido a fatiga mecánica y térmica. Por otra parte, para conseguir el llenado completo del molde en los tiempos indicados, es necesario que el material fluya a velocidades considerables y dada la geometría compleja de las piezas a obtener, nunca es posible conseguir un flujo laminar del fluido, por lo que se produce un efecto de desgaste de la superficie del molde, (ayudado además por la reactividad química del Al con el acero), en el que se combinan los efectos principales que producen este fenómeno, es decir:
· Desgaste por adherencia.
· Desgaste por abrasión.
· Desgaste por fatiga.
· Desgaste por cavitación.
· Desgaste por corrosión.
Según esto, es determinante el estado metalúrgico de la superficie de la herramienta y su coherencia y continuidad con el núcleo de la misma, a fin de garantizar el comportamiento durante el trabajo, será pues necesario que el tratamiento térmico permita la mayor homogeneidad posible a nivel microestructural y de tensiones residuales y evite el cambio químico superficial durante el proceso térmico.
Sistemas de Temple a alta presión con parada Isotérmica (TEMPLE interrumpido o Martempering).
Para responder a la problemática expuesta, el tratamiento térmico debe ser lo más enérgico posible. En función de esta finalidad, los modernos hornos de tratamiento en vacío disponen de la posibilidad de templar con altas presiones de gas (hasta 10-20 bares). pero un proceso de temple con enfriamiento continuo, utilizando una velocidad de temple muy elevada, comporta un alto riesgo de aparición de grietas y de fuerte distorsión de la pieza templada.
Estos problemas son especialmente críticos en pieza de geometría compleja como son los moldes de fundición inyectada. La solución a este problema es el temple con parada isotérmica (martempering) ya utilizado en las instalaciones de sales y de las modernas instalaciones de vacío permiten realizar utilizando las características de enfriamiento acelerado a alta presión y mantenimiento por convección a baja temperatura. Los diagramas siguientes, muestran un proceso de martempering realizado sobre una pieza de dimensiones 360x420x150 mm (promedio) en material 1.2343.
Como resumen expondremos en una tabla las necesidades y requerimientos de una moderna instalación de tratamiento térmico al vacío orientada al siempre complejo problema del tratamiento de moldes y matrices.
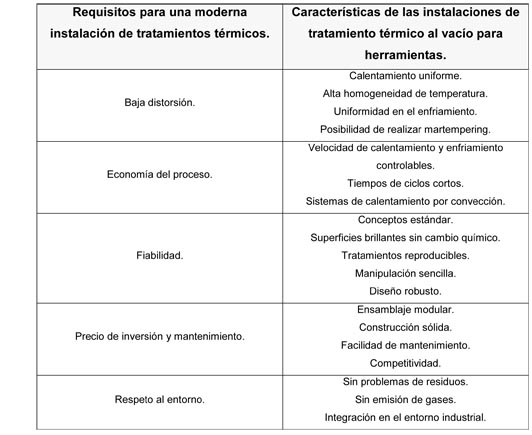
Un ejemplo de instalación moderna de vacío se muestra en la foto siguiente:
Finalmente es necesario destacar la necesidad de control de los procesos llevados a cabo en una planta de tratamiento térmico.
Resultados obtenidos de los ensayos a nivel industrial utilizando los medios propios de la empresa
Para contrastar lo expuesto hasta el momento, se han realizado ensayos a nivel industrial utilizando los medios propios de la empresa desde el punto de vista de instalaciones de tratamiento térmico y de laboratorio. Dentro de estos últimos, se ha utilizado la experiencia obtenida en el marco del proyecto europeo antes mencionado: CRAFT “TOOLSLIFE”. Se han colocado tres probetas de resilencia por cada ensayo en el núcleo de una pieza de forma que simulen las condiciones más perjudiciales en cuanto a velocidad de enfriamiento. Sobre estas probetas se ha realizado ensayo de resilencia y micrografías SEM a 5, 10 y 15 mil aumentos. Se han realizado también tres probetas de cada tratamiento para la realización de ensayo KIC utilizando la probeta de flexión E-399 ASTM de 25 mm de espesor. Así mismo se han realizado ensayos para obtener el valor KIC mediante la máquina prototipo desarrollada en el proyecto CRAFT mencionado (figura a continuación): Resiliómetro.
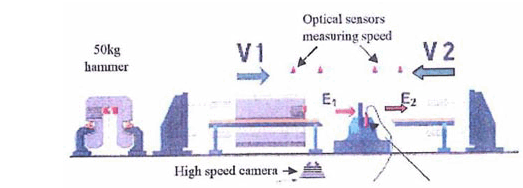
Los resultados obtenidos han sido los siguientes:
Dureza:
Proceso 1
(Temple a 4 bar absolutos con martempering a 450ºC + 3R), Dureza 45-46 HRC Proceso 2
(Temple en sales con apagado isotérmico a 550ºC + 3R), Dureza 45-46 HRC Proceso 3
(Temple a 2 bar absolutos enfriamiento continuo + 3R), Dureza 45-46 HRC
Microestructuras:
En todos los casos se aprecia una estructura de martensita revenida con una cierta precipitación de carburos en borde de grano que es mayor en las probetas correspondientes a los tratamientos 2 y 3, siendo de resaltar el tipo de carburos presentes en estos dos últimos procesos con morfologías que indican una precipitación causada por velocidad de enfriamiento algo escasa (ver micrografías).
Ensayos de Resiliencia:
Los valores de resilencia son los siguientes: Tratamiento 1 – 16, 18, 16 Joules Tratamiento 2 – 13, 14, 17 Joules Tratamiento 3 – 12, 16, 15 Joules
Valores de KIC:
Los valores de KIC obtenidos mediante la probeta de flexión E-399 ASTM, son los siguientes: Tratamiento 1 – 55 MN/m3/2 Tratamiento 2 – 47 MN/m3/2 Tratamiento 3 –49 MN/m3/2 Los valores obtenidos mediante el resiliometro son los siguientes (no disponemos de datos para las probetas templadas en sales, Tratamiento 2): Tratamiento 1 – 53.8 MN/m3/2 Tratamiento 3 – 51.5 MN/m3/2
conclusiones
Tanto los valores obtenidos como los resultados micrográficos, indican que el mejor tratamiento posible es el temple interrumpido con enfriamiento a alta presión. Ensayos realizados en S.A. Metalográfica con enfriamiento continuo y 6 bar de presión absoluta proporcionan valores de resilencia más altos (20 a 25 Joules) pero no disponemos de los valores correspondientes de KIC, sin embargo la distorsión del molde es considerablemente superior lo que penaliza la acumulación de tensiones y la posible disminución de la duración del molde además de un mayor coste de fabricación. Teniendo en cuenta que el valor considerado como correcto para estos materiales es de 14 Joules podemos concluir que el tratamiento con parada isotérmica realizado en los modernos hornos de vacío es el más adecuado para obtener la mejor duración de vida de las herramientas y en concreto de los moldes de trabajo en caliente. La utilización del “resiliometro” (desarrollado dentro del proyecto europeo CRAFT) ha sido muy útil para poder obtener valores de KIC de una forma relativamente cómoda. Los valores obtenidos de KIC mediante los 2 sistemas (probeta ASTM y “resiliometro”) son bastante concordantes y parecen ratificar lo enunciado anteriormente: El tratamiento a alta presión, con parada isotérmica, parece ser el mejor tratamiento para utillajes sometidos a altas solicitaciones, como pueden ser los moldes para fundición inyectada de aleaciones ligeras (aluminio).
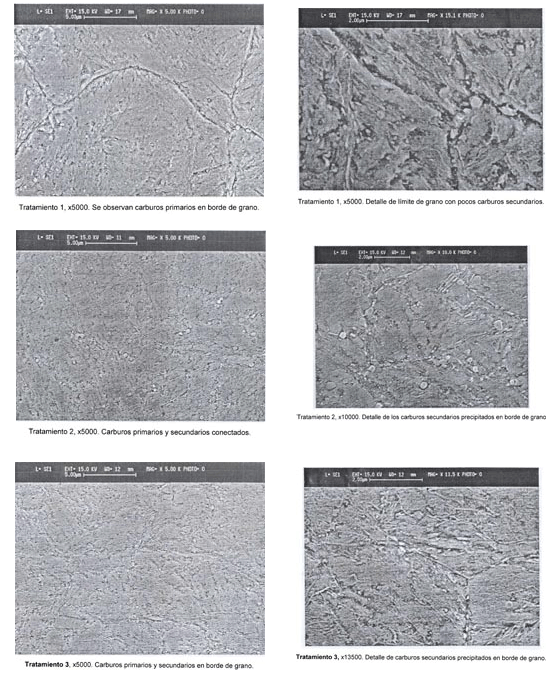
|
|
DURPLAN
Tel. 93 861 60 77
Fax. 93 861 60 78
|
|
|
|
|
|
|
home |
|
|
|
|
|
tabla de durezas |
|
|