autores: Fidel Zapiráin, Fidel Zubiri, Fermín Garciandía, Itziar Tolosa.
LORTEK
Estudio del proceso y propiedades obtenidas en un inserto fabricado por aporte de material por láser en un utillaje para conformado metálico
Los procesos de aporte de material están abriendo nuevas posibilidades de fabricación en distintos ámbitos, comenzando por los de reparación superficial en componentes de alto valor, hasta la fabricación aditiva de componentes complejos, pasando por la aplicación de capas de altas prestaciones. Actualmente hay aplicaciones de éxito en sectores industriales como el aeronáutico, el de moldes y matrices y el de consumo.
La utilización del láser para realizar aplicaciones de aporte de material presenta una serie de ventajas inherentes a las propiedades de esta forma de fuente de energía. Cabe señalar que los componentes que son reparados, recubiertos o fabricados por aporte de energía son componentes de valor y, por tanto, fabricados con aleaciones de altas prestaciones con propiedades muy definidas y que no se pueden perder en sus procesos de fabricación. Una de las ventajas del láser es la posibilidad de ser enfocado en zonas muy localizadas afectando térmicamente de forma muy limitada a las zonas de material próximas a la zona aportada.
Características generales
Los procesos de aportación por láser (o “laser cladding") utilizan, en general, materiales de aporte en forma de polvo, aunque también se utilizan en forma de hilo. En la fotografía correspondiente a la figura 1 se muestra un detalle del proceso de aporte de material en forma de polvo con una boquilla coaxial (figura de la boquilla aportando en un trozo de matriz). El material de aporte en forma de polvo es llevado a la boquilla donde el láser lo funde, junto a la capa más superficial del material donde se deposita; de esta forma, se obtienen capas densas y compactas unidas metalúrgicamente con el material base.
En este artículo se recogen los resultados obtenidos en un demostrador (punzón), fabricado con una fundición de hierro (laminar y esferoidal) sobre el que se ha fabricado un inserto en acero de alta resistencia antifricción (acero rápido M2) mediante aporte sucesivo de capas de material por láser.
Estudio experimental
Se planteó la posibilidad de obtener un punzón –fabricado con diferentes fundiciones férricas- para procesos de conformado en frío con un “inserto” de muy alta dureza en una zona definida del mismo (figura 1). La solución planteada fue fabricar el inserto por aporte láser. Para ello se fabricó un demostrador de dicho punzón por un proceso convencional de moldeo y mecanizado, dejando vacía la zona a ser crecida mediante aporte por láser (figura 2).
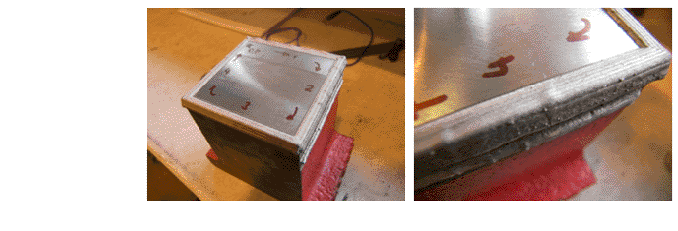
El estudio comenzó con los materiales seleccionados: el base es una fundición de hierro (primero una fundición gris laminar y, posteriormente, una nodular) y el inserto un acero rápido de muy alta dureza (M2, 60 HRC) sobre una capa más dúctil (capa “colchón, de aleación de Ni), buscando alargar la vida del útil al conformar chapa de aceros de alta resistencia.
Las pruebas de aporte de material se han realizado con un láser de diodos, de 3 kW de potencia, focalizado en la zona de aporte en un “spot” de 1.5 mm de diámetro. Se ha utilizado para el proceso una boquilla coaxial (figura 3). La trayectoria del proceso de aporte se ha programado por CNC. El proceso de aporte es asistido por gas argón aportado a través de la boquilla coaxial. Con esta disposición se han realizado diferentes series de pruebas experimentales, variando velocidad de proceso, potencia, solapamiento entre cordones y caudal de aporte de polvo. Finalmente, se han seleccionado, en este caso, los siguientes parámetros:
- Potencia: 800 y 1800 W.
- Velocidad: 500 mm/min.
- Caudal de polvo: 6 y 12 g/min.
- Anchura de cordón individual: 1,5 y 3,2 mm.
- Solapamiento entre cordones: 33 %.
El resultado obtenido en el proceso de laser cladding está muy ligado a los materiales involucrados. A diferencia de los procesos de soldadura en los que el material de aporte es similar al material base, en los procesos de aporte, cuando se ponen capas de altas prestaciones, es común que el material base y de aporte sean muy diferentes; por lo tanto, en casos en los que no hay una experiencia previa contrastada es necesario hacer un estudio de viabilidad del proceso con los materiales involucrados.
En este caso, se comenzó realizando pruebas experimentales de aporte láser sobre e l material base y otras mas referidas a caracterización experimental mediante análisis metalográfico.
En la macrografía correspondiente a la figura 4, se muestra uno de los recargues realizados, en los que se aprecian tanto las capas colchón como las capas más externas de material duro y resistente.
Se aprecia la compacidad de las capas, las bajas diluciones y la ausencia de defectos en las capas depositadas.
En la inspección por líquidos penetrantes y análisis metalográfico, se han observado grietas en los recargues realizados sobre fundición laminar. Estas grietas en forma de desgarre se han observado en las zonas de inicio y final de las zonas aportadas (figura 5). En el caso de la fundición esferoidal no se han observado estos problemas (figura 5).
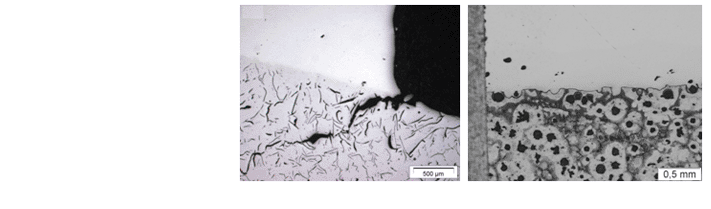
Asimismo, se han realizado barridos de medidas de microdureza (Vickers) en las muestras recargadas en intervalos de 0,2 mm. En la figura 6 se muestran los resultados obtenidos, y en la que se puede apreciar los altos niveles de dureza conseguidos en la capa superficial en algunas de las muestras experimentales obtenidas.
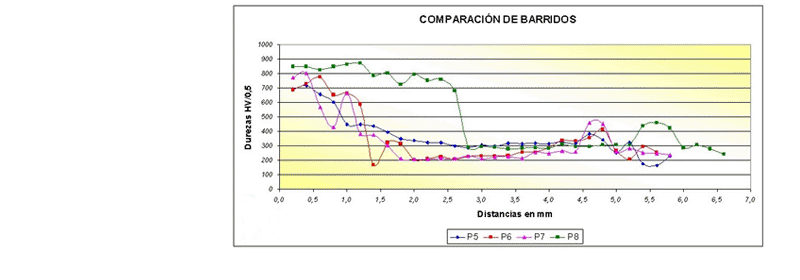
Conclusiones
De todo lo expuesto, se derivan las siguientes conclusiones:
- El objetivo de este estudio ha sido el de analizar la aplicación del proceso de material de aporte en determinados modelos de utillaje de conformado de chapa metálica.
- La función definida de proceso de aporte ha sido, por una parte, obtener localmente una zona de altas prestaciones (muy superiores a las del material base con el que está hecho el útil) y, por otro, poder disponer de una herramienta de reparación cuando el utillaje empiece a mostrar síntomas de deterioro.
- Los materiales base analizados han sido una fundición laminar y una esferoidal. Se han realizado aportes con material duro y, en algunos casos, introduciendo una “capa colchón”, dúctil, para hacer viable el proceso.
- Para realizar el proceso se ha utilizado un láser de diodos directo, un alimentador de material en forma de polvo y una boquilla coaxial.
- La fundición laminar muestra fisuras en forma de desgarre en gran cantidad de las pruebas realizadas.
- Los aportes realizados sobre la fundición nodular no han mostrado defectos.
- Las durezas máximas alcanzadas en la capa exterior, utilizando un acero rápido, han superado los 800 HV en algunas de las referencias realizadas.
LORTEK
Centro de investigación en tecnologías de unión E-mail:lortek@lortek.es
www.lortek.es
|